Sensors¶
Sensors section allows to configure any sensor connected or internal from 1x autopilot.
Accelerometer¶
1x autopilot incorporates 3 Inertial Measurement Units (IMUs) that allows the 1x system to measure different variables and that are the main navigation data source. From the IMU, the user can configure the Accelerometer and Gyroscope. The first one is explained below.
The user can choose between 3 types of source for the accelerometer:
Internal (Secondary/BMI088/ADIS16505-3 Accelerometer): 1x autopilot uses the internal sensor.
Warning
If the user has a 1x autopilot with
hardware version 4.5
, the Main Accelerometer is available instead of the ADIS16505-3 Accelerometer, which has the same configurable parameters as the Secondary Accelerometer.Integer var sensor 1-2: 1x autopilot uses a integer value provided by an external sensor.
Decimal var sensor 1-2: 1x autopilot uses a decimal value provided by an external sensor.
Suggestion
Depending on the hardware version, the following accelerometer is suggested:
4.5 version
BMI088 Accelerometer4.8 version
ADIS16505-3 Accelerometer
Secondary Accelerometer
This menu displays the posible parameters that can be configured for the internal Secondary Accelerometer.
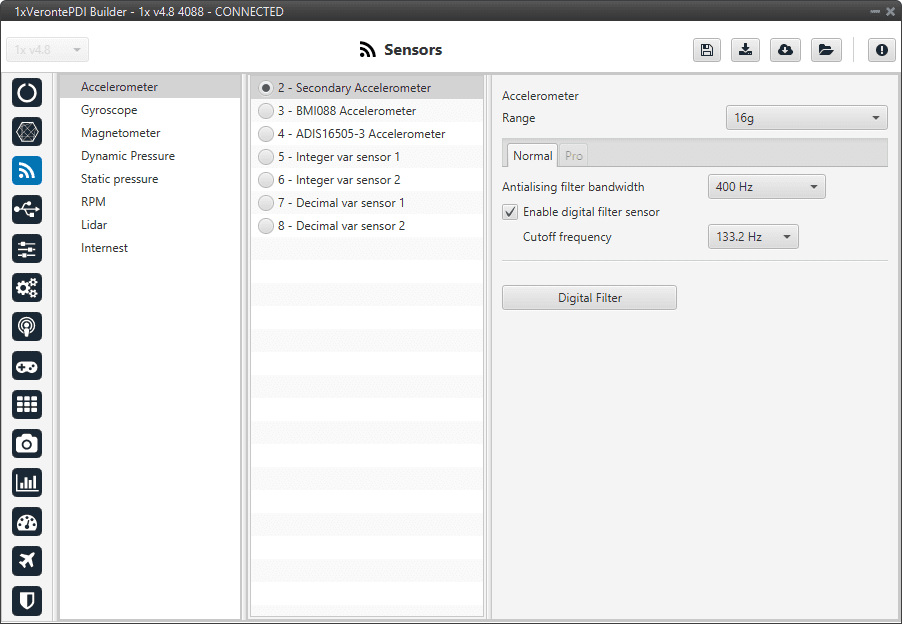
Secondary Accelerometer menu¶
In this menu it is possible to set different options regarding range and filters from the accelerometer. The parameters that can be modified are:
Range: Selectable range of forces that the accelerometer can measure, high ranges implies less precision while small ranges might mean the system saturates. Values allowed are 2g, 4g, 8g and 16g.
Anatialising filter bandwith: It is the bandwidth of the antialiasing low pass filter. The options available are 50Hz, 100Hz, 200Hz and 400Hz, the greater the value selected the worse the filtering will be.
Enable digital filter sensor: Enables a low pass filter which its cutoff frequency is configured from the options 16.65Hz, 66.6Hz, 133.2Hz and 740.0Hz. This is a hardware filter, included directly in the accelerometer.
Digital filter: Enables a low pass filter which its cutoff frequency is configured manually, allowing the user to input any desired value in Hz. It is a software filter, applied after the hardware filter from the point before.
BMI088 Accelerometer
This menu displays the posible parameters that can be configured for the internal BMI088 Accelerometer.
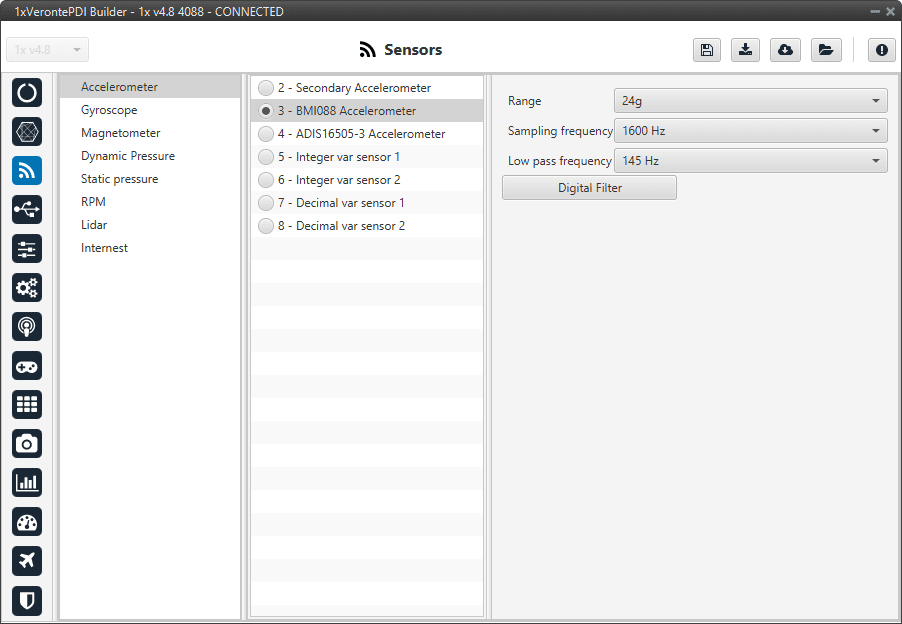
BMI088 Accelerometer menu¶
In this menu it is possible to set different options regarding range and filters from the accelerometer. The parameters that can be modified are:
Range: Selectable range of forces that the accelerometer can measure, high ranges implies less precision while small ranges might mean the system saturates. Values allowed are 3g, 6g, 12g and 24g.
Sampling frequency: That is the frequency at which the measurements are read out. Values allowed are 12.5Hz, 25Hz, 50Hz, 100Hz, 200Hz, 400Hz, 800Hz and 1600Hz. We recommend the highest.
Low pass frequency: This is a hardware filter, included directly in the accelerometer, which its cutoff frequency is configured from the options 145Hz, 234Hz (215Hz for Z axis) and 280Hz (245Hz for Z axis).
Digital filter: Enables a low pass filter which its cutoff frequency is configured manually, allowing the user to input any desired value in Hz. It is a software filter, applied after the hardware filter from the point before.
ADIS16505-3 Accelerometer
This menu displays the posible parameters that can be configured for the internal ADIS16505-3 Accelerometer.
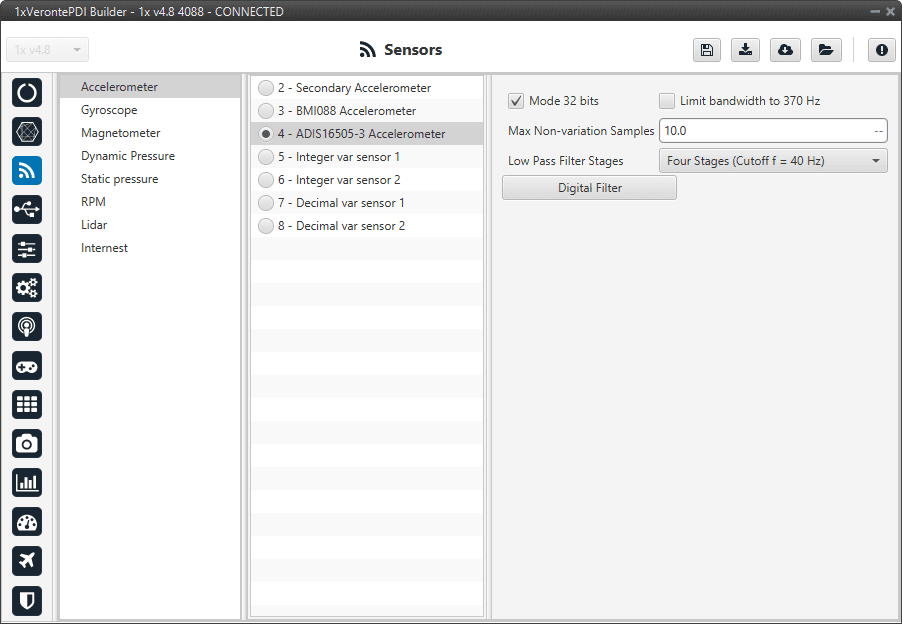
ADIS16505-3 Accelerometer menu¶
In this menu it is possible to set different options regarding range and filters from the accelerometer. The parameters that can be modified are:
Mode 32 bits: Enable or disable. With 32 bits of precision. We recommend enabling it.
Limit bandwith to 370Hz: Enable or disable. It can only be used without using a Low Pass Filter Stages. We recommend disabling it.
Max Non-variation Samples: It is configured manually.
Low Pass Filter Stages: IMU’s Hardware filter. The options available are:
No filter
1 stage (Cutoff f=364Hz)
2 stages (Cutoff f=165Hz)
3 stages (Cutoff f=80Hz)
4 stages (Cutoff f=40Hz)
5 stages (Cutoff f=20Hz)
6 stages (Cutoff f=10Hz)
We recommend 4 stages (Cutoff f=40Hz) option.
Digital filter: Enables a low pass filter which its cutoff frequency is configured manually, allowing the user to input any desired value in Hz.
Warning
It is recommended to choose the hardware filter (Low Pass Filter) except if a lower cutoff frequency is needed (< 10 Hz).
It is not recommended flying without a filter.
Integer var sensor 1-2
In this menu it is possible to configure integer variables provided by an external sensor.
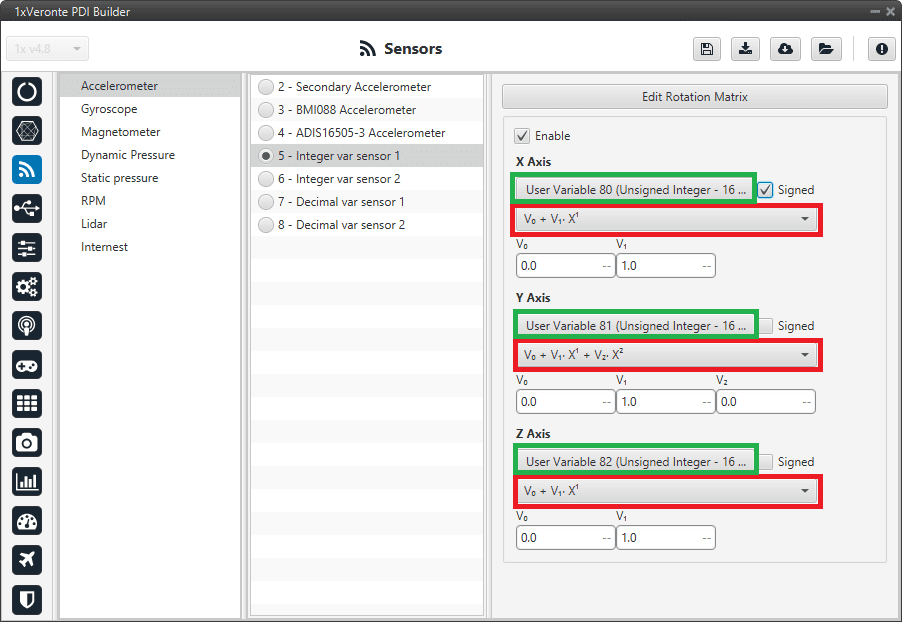
Integer var accelerometer sensor menu¶
When Integer var sensor 1 or 2 are selected, the previous panel will be shown. In this panel, the user selects the variable that has been stored in a user variable (Green Box) and the operations that will be carried on (Red Box). It is possible to use the signal through a linear or quadratic relation. The following image shows an example of a linear relation:
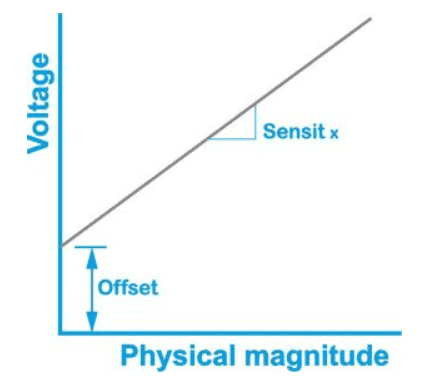
Linear relation of 2 variables¶
In addition, users must indicate whether the integer value is with sign or without sign. That is, if the “Signed” box is:
Enabled: Integer value with sign.
Disabled: Integer value without sign.
The process of configuration has to be done using custom messages. This is to be configured in the Custom Messages menu of the I/O section. The configuration will depends on the device in use and its communication protocol.
Warning
Edit Rotation Matrix brings the position of the accelerometer inside the 1x autopilot, it must NOT be changed under any circumstance.
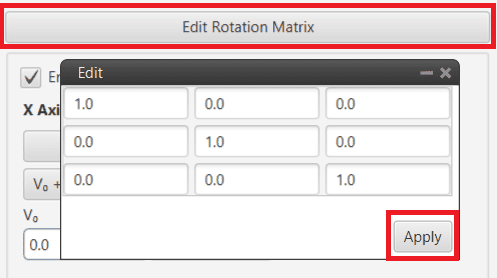
Rotation matrix¶
Decimal var sensor 1-2
In this menu, the user selects real variables for each axis (X,Y,Z), these do not requiere a signal treatment. The process of configuration is similar to the one carried out when configuring a Integer Variable.
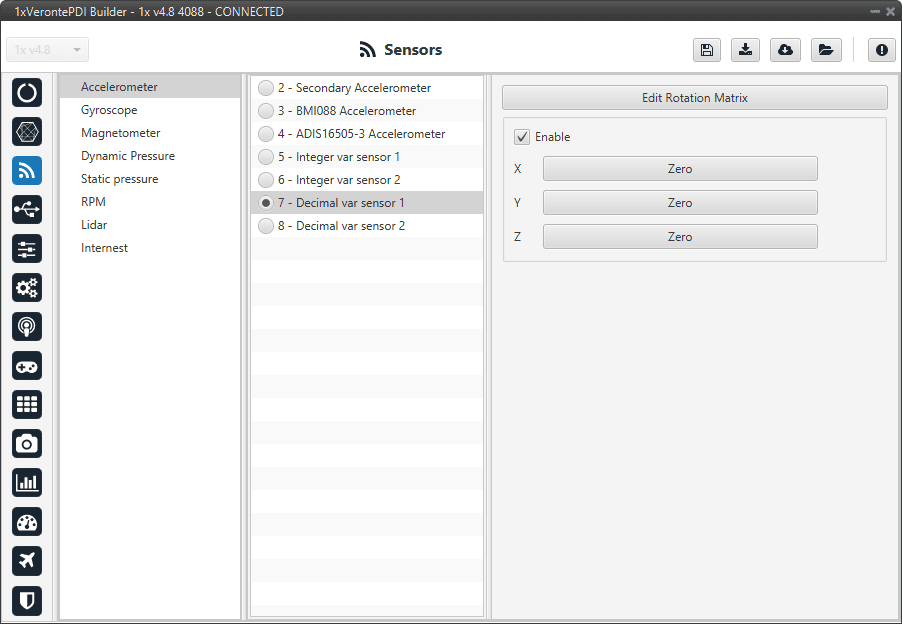
Decimal var accelerometer sensor menu¶
Gyroscope¶
The gyroscope from the IMU can be configured as explained in the menus shown below.
The user can choose between 3 types of source for the gyroscope:
Internal (Secondary/BMI088/ADIS16505-3 Gyroscope): 1x autopilot uses the internal sensor.
Warning
If the user has a 1x autopilot with hardware version 4.5, the Main Gyroscope is available instead of the ADIS16505-3 Gyroscope, which has the same configurable parameters as the Secondary Gyroscope.
Integer var sensor 1-2: 1x autopilot uses a integer value provided by an external sensor.
Decimal var sensor 1-2: 1x autopilot uses a decimal value provided by an external sensor.
Suggestion
Depending on the hardware version, the following gyroscope is suggested:
4.5 version
BMI088 Gyroscope4.8 version
ADIS16505-3 Gyroscope
Secondary Gyroscope
This menu displays the posible parameters that can be configured for the internal Secondary Gyroscope.
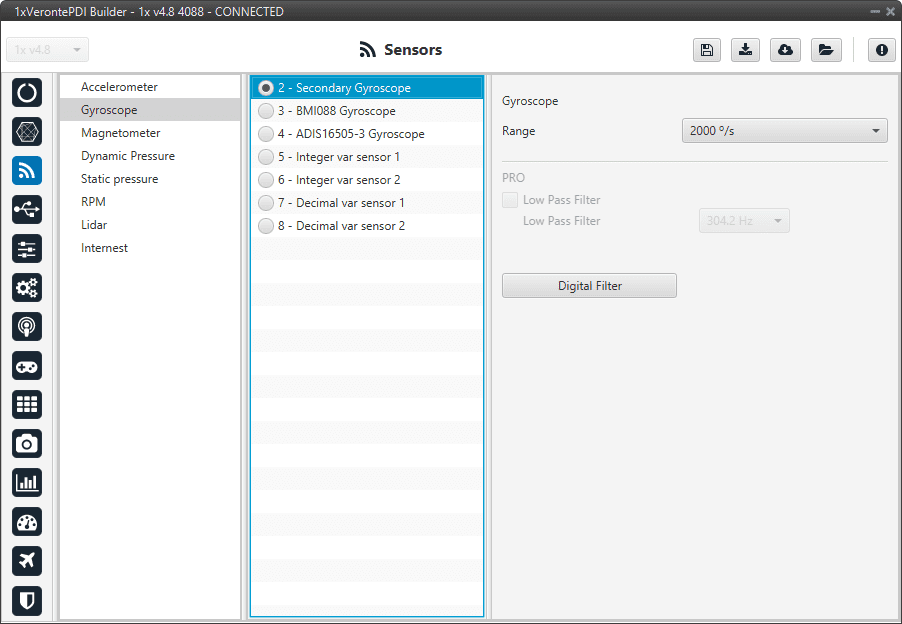
Secondary Gyroscope menu¶
In this menu it is possible to set different options regarding range and filters from the gyroscope. The parameters that can be modified are:
Range: Sets the maximum range of performance, high ranges implies less precision while small ranges might mean the system saturates. Values allowed are 125°/s, 250°/s, 500°/s, 1000°/s and 2000°/s.
Digital filter: Enables a low pass filter which its cutoff frequency is configured manually, allowing the user to input any desired value in Hz. It is a software filter.
BMI088 Gyroscope
This menu displays the posible parameters that can be configured for the internal BMI088 Gyroscope.
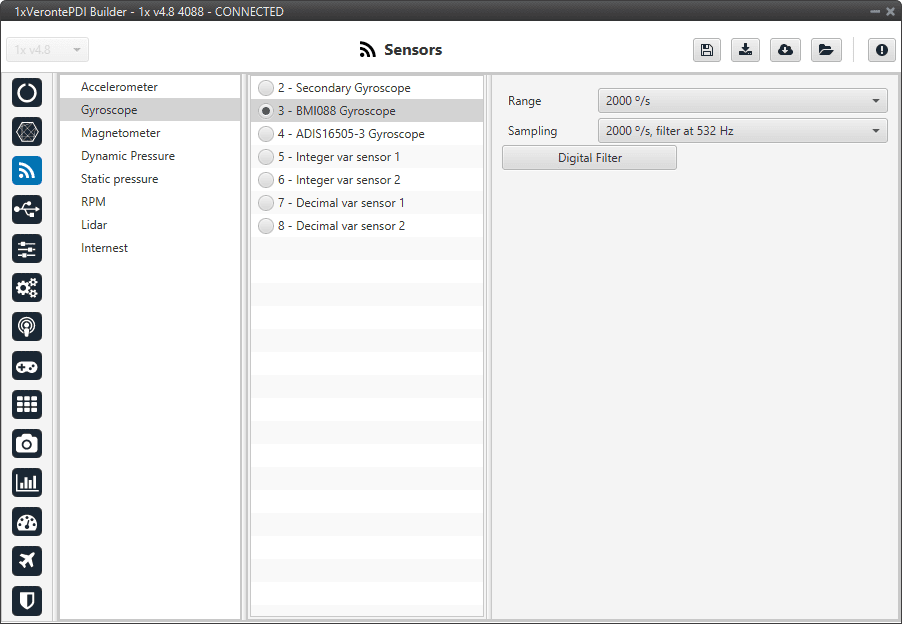
BMI088 Gyroscope menu¶
In this menu it is possible to set different options regarding range and filters from the gyroscope. The parameters that can be modified are:
Range: Sets the maximum range of performance, high ranges implies less precision while small ranges might mean the system saturates. Values allowed are 125°/s, 250°/s, 500°/s, 1000°/s and 2000°/s.
Sampling: That is the angular velocity at which the measurements are read out. Values allowed are 100°/s filter at 32 Hz, 200°/s filter at 64 Hz, 100°/s filter at 12 Hz, 200°/s filter at 32 Hz, 400°/s filter at 47 Hz, 1000°/s filter at 116 Hz, 2000°/s filter at 230 Hz and 2000°/s filter at 532 Hz.
Digital filter: Enables a low pass filter which its cutoff frequency is configured manually, allowing the user to input any desired value in Hz. It is a software filter.
ADIS16505-3 Gyroscope
This menu displays the posible parameters that can be configured for the internal ADIS16505-3 Gyroscope.
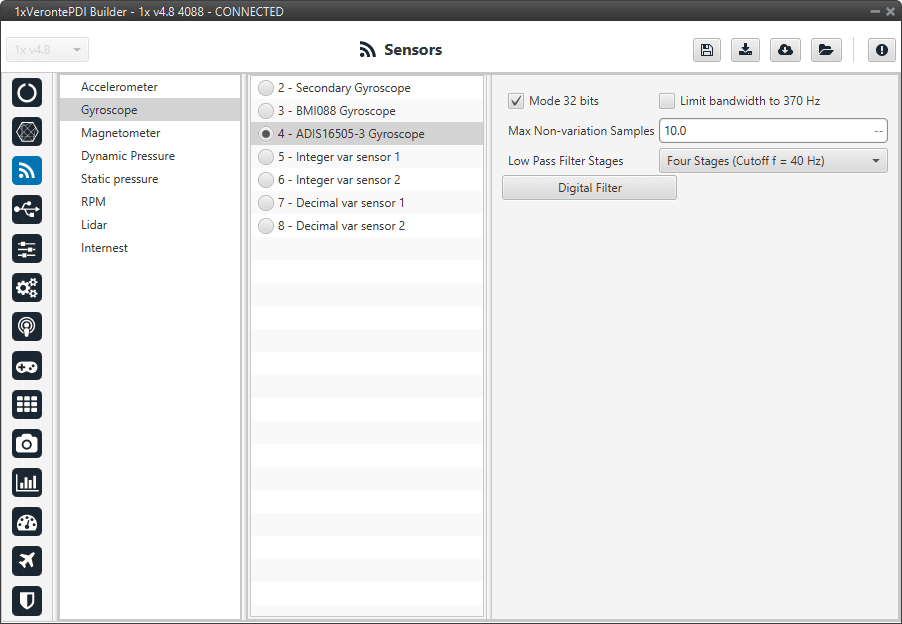
ADIS16505-3 Gyroscope menu¶
In this menu it is possible to set different options regarding range and filters from the gyroscope. The parameters that can be modified are:
Mode 32 bits: Enable or disable. With 32 bits of precision. We recommend enabling it.
Limit bandwith to 370Hz: Enable or disable. It can only be used without using a Low Pass Filter Stages. We recommend disabling it.
Max Non-variation Samples: It is configured manually.
Low Pass Filter Stages: The options available are No filter, 1 stage (Cutoff f=364Hz), 2 stages (Cutoff f=165Hz), 3 stages (Cutoff f=80Hz), 4 stages (Cutoff f=40Hz), 5 stages (Cutoff f=20Hz) and 6 stages (Cutoff f=10Hz). We recommend 4 stages (Cutoff f=40Hz).
Digital filter: Enables a low pass filter which its cutoff frequency is configured manually, allowing the user to input any desired value in Hz. We recommend disabling it.
Warning
It is not recommended flying without a filter.
Integer var sensor 1-2
In this menu it is possible to configure integer variables provided by an external sensor.
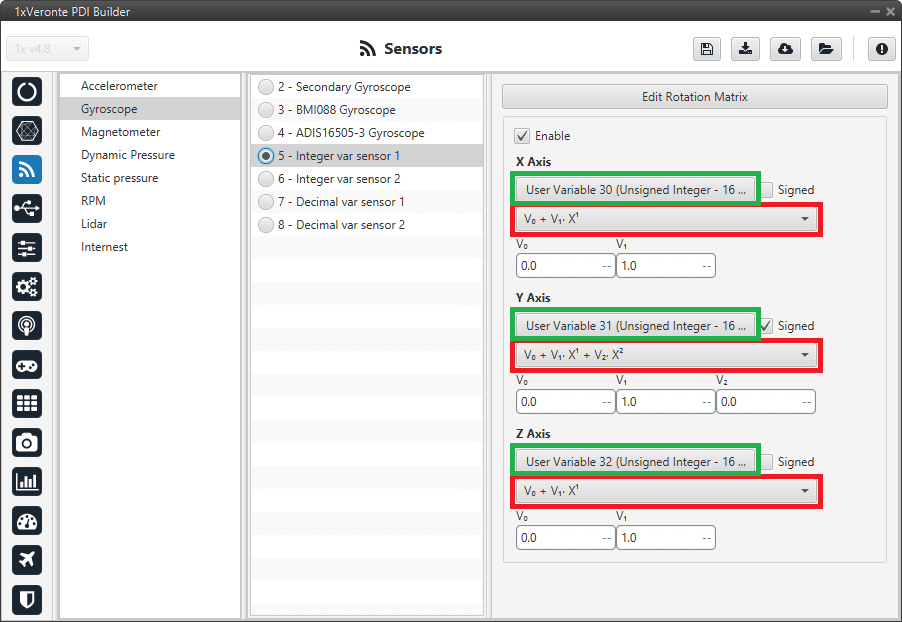
Integer var gyroscope sensor menu¶
When Integer var sensor 1 or 2 are selected, the previous panel will be shown. In this panel, the user selects the variable that has been stored in a user variable (Green Box) and the operations that will be carried on (Red Box). It is possible to use the signal through a linear or quadratic relation. The following image shows an example of a linear relation:
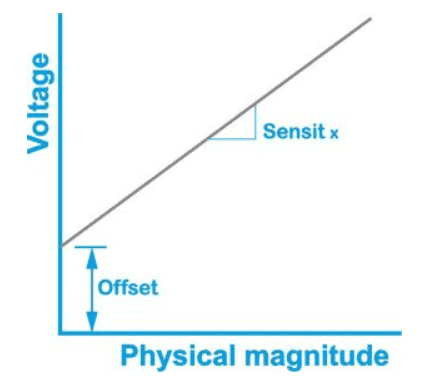
Linear relation of 2 variables¶
In addition, users must indicate whether the integer value is with sign or without sign. That is, if the “Signed” box is:
Enabled: Integer value with sign.
Disabled: Integer value without sign.
The process of configuration has to be done using custom messages. This is to be configured in the Custom Messages menu of the I/O section. The configuration will depends on the device in use and its communication protocol.
Warning
Edit Rotation Matrix brings the position of the gyroscope inside the 1x Autopilot, it must NOT be changed under any circumstance.
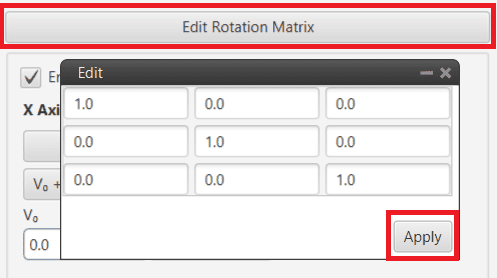
Rotation matrix¶
Decimal var sensor 1-2
In this menu, the user selects real variables for each axis (X,Y,Z), these do not requiere a signal treatment. The process of configuration is similar to the one carried out when configuring a Integer Variable.
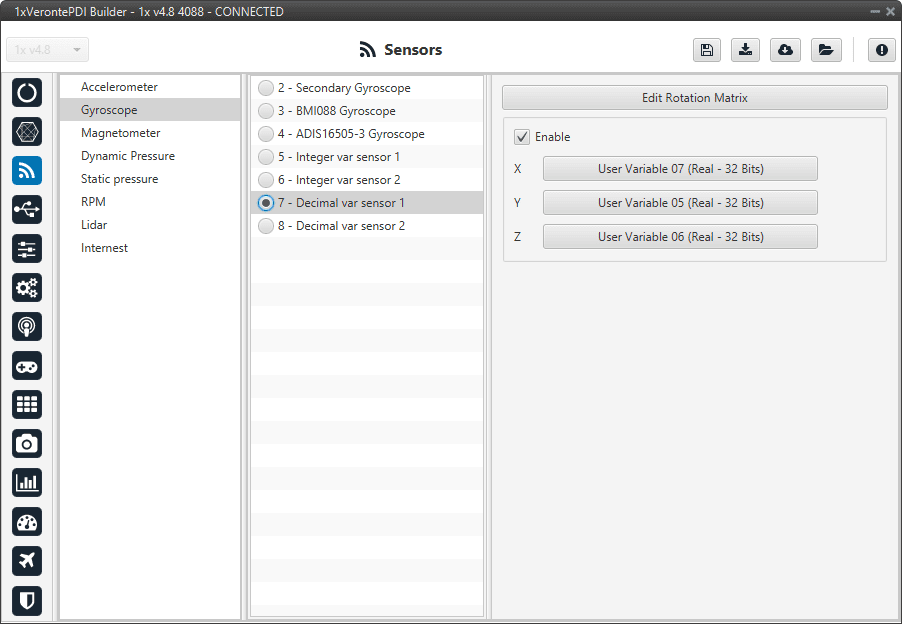
Decimal var gyroscope sensor menu¶
Magnetometer¶
1x autopilot incorporates an internal magnetometer that allows the 1x System to measure the magnetic field.
The user can choose between 4 types of source for the magnetometer.
Internal(LIS3MDL/MMC5883MA/RM3100): 1x autopilot uses the internal sensor.
Warning
If the user has a 1x autopilot with hardware version 4.5, Internal RM3100 Magnetometer is not available.
Integer var sensor 1-2: 1x autopilot uses a integer value provided by a no-integrated external sensor.
Decimal var sensor 1-2: 1x autopilot uses a decimal value provided by a no-integrated external sensor.
External (HMR2300/LIS3MDL/HSCDTD008A/MMC5883MA/RM3100): 1x autopilot uses the information from one of the compatible external magnetometers.
For this sensor, it is possible to have more than one selected for the navigation algorithm, so the user will have redundancy in magnetometer sensor.
Suggestion
Depending on the hardware version, the following magnetometer is suggested:
4.5 version
Internal MMC5883MA Magnetometer4.8 version
Internal RM3100 Magnetometer
Note
LIS3MDL and HSCDTD008A Magnetometer are integrated in 1x autopilot with the I2C interface. They are inside the 1x, but mounted externally to avoid the possible interferences from being close to electronic components.
Magnetometer LIS3MDL: It is a three-axis magnetic sensor with a very small package.
Magnetometer HSCDTD008A: It is a three-axis terrestrial magnetism sensor of the digital output.
It is very important to know that address cannot be chosen in the software and must be as follows:
Magnetometer LIS3MDL: 0x1C.
Magnetometer HSCDTD008A: 0x0C.
Important
In this section, the user can only modify some configurable parameters, the selection of the magnetometer and the configuration of the Variance are done in Magnetometer sensor - Block Programs section.
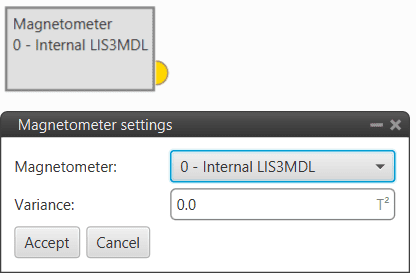
Magnetometer block¶
Internal LIS3MDL/MMC5883MA/RM3100
This menu available displays the posible parameters that can be configured for the internal Magnetometer.
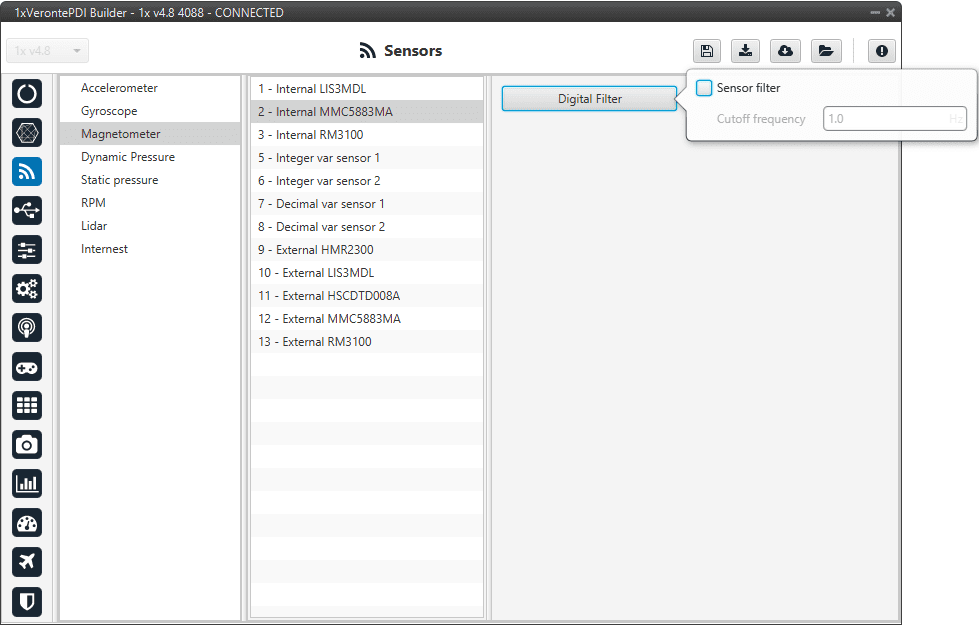
Internal Magnetometer menu¶
In this menu it is possible to modify different options regarding the digital filter:
Digital filter: Enables a low pass filter which its cutoff frequency is configured manually, allowing the user to input any desired value in Hz. It is a software filter.
Integer var sensor 1-2
In this menu it is possible to configure integer variables provided by an external sensor.
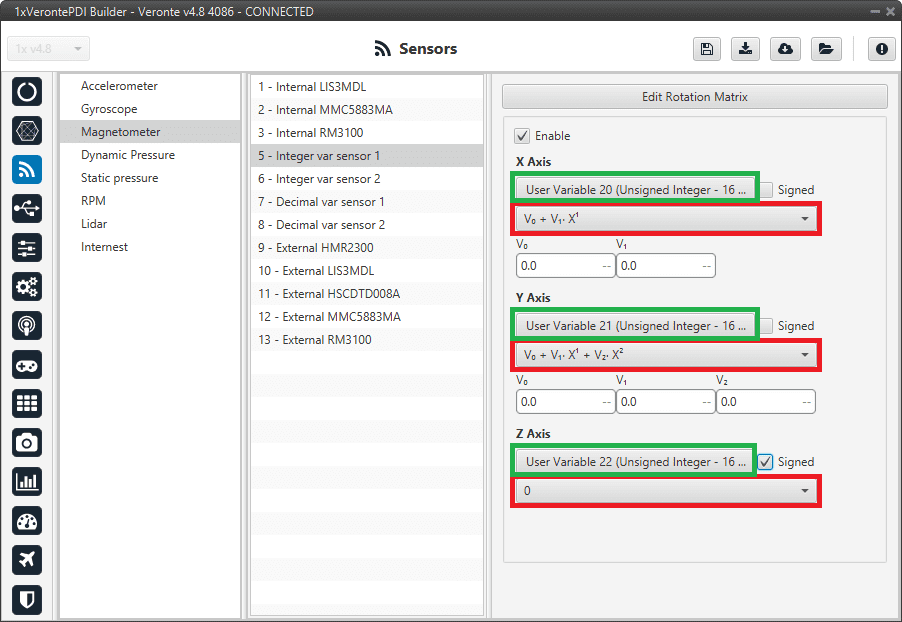
Integer var magnetometer sensor menu¶
When Integer var sensor 1 or 2 are selected, the previous panel will be shown. In this panel, the user selects the variable that has been stored in a user variable (Green Box) and the operations that will be carried on (Red Box). It is possible to use the signal through a linear or quadratic relation. The following image shows an example of a linear relation:
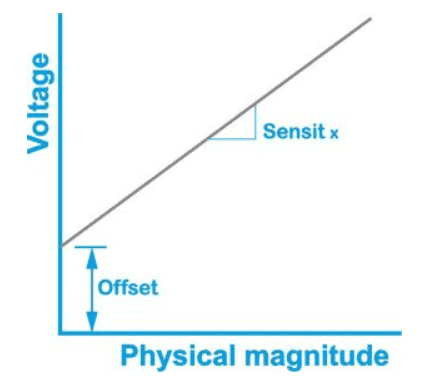
Linear relation of 2 variables¶
In addition, users must indicate whether the integer value is with sign or without sign. That is, if the “Signed” box is:
Enabled: Integer value with sign.
Disabled: Integer value without sign.
The process of configuration has to be done using custom messages. This is to be configured in the Custom Messages menu of the I/O section. The configuration will depends on the device in use and its communication protocol.
Warning
Edit Rotation Matrix brings the position of the magnetometer inside the 1x Autopilot, it must NOT be changed under any circumstance.
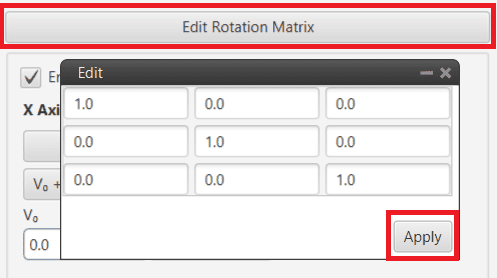
Rotation matrix¶
Decimal var sensor 1-2
In this menu, the user selects real variables for each axis (X,Y,Z), these do not requiere a signal treatment. The process of configuration is similar to the one carried out when configuring a Integer Variable.
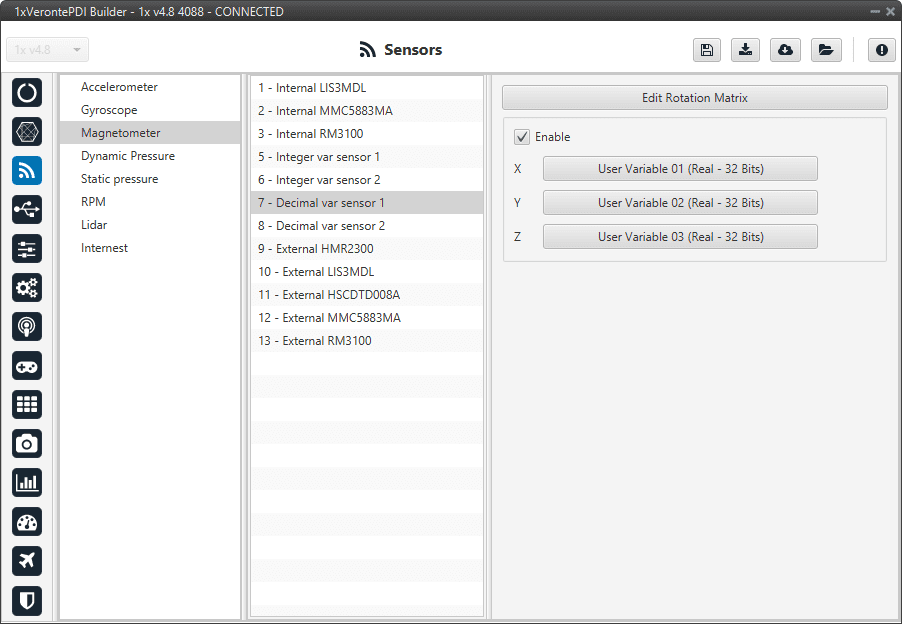
Decimal var magnetometer sensor menu¶
External HMR2300
1x autopilot has been designed to have compatibility with this external magnetometer.
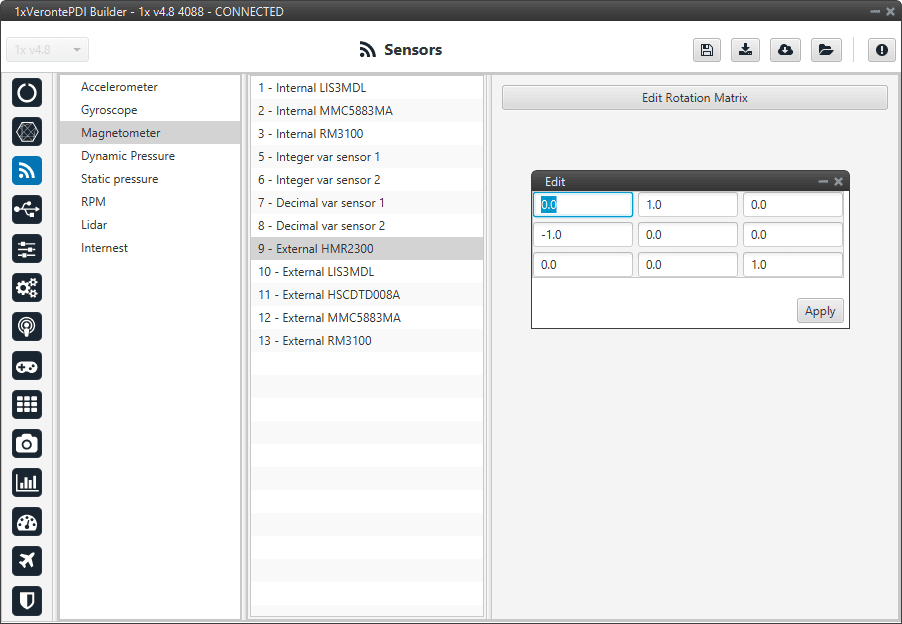
External HMR2300 Magnetometer menu¶
This magnetometer has no filters configurable, only the option Edit Rotation Matrix to set the orientation of it.
On the other hand, the connection to the serial port has to be configured in the I/O Setup section of the I/O menu.
External LIS3MDL/HSCDTD008A/MMC5883MA/RM3100
1x autopilot has been designed to have compatibility with this external magnetometer.
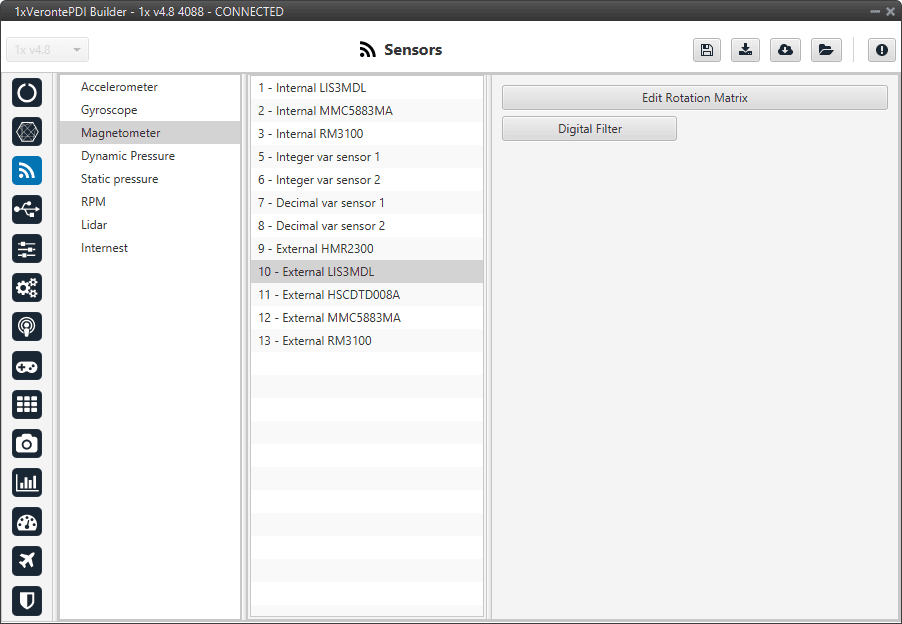
External Magnetometer menu¶
The user can modify the following parameters:
Rotation matrix: It must be modified in the case that the axes of the magnetometer do not coincide with those of the aircraft.
Digital filter: Enables a low pass filter which its cutoff frequency is configured manually, allowing the user to input any desired value in Hz. It is a software filter.
Dynamic Pressure¶
1x autopilot has three pressure input lines, two for static pressure to determine the absolute pressure and one for pitot in order to determine the dynamic pressure.
This menu allows the user to configure a Dynamic Pressure sensor input in 1x.
The user can choose between 3 types of source:
Internal: 1x autopilot uses the internal sensor.
Integer var sensor 1-2: 1x autopilot uses a integer value provided by an external sensor.
Decimal var sensor 1-2: 1x autopilot uses a decimal value provided by an external sensor.
Navigation
The Navigation menu has 5 parameters that are configured independently from the Dynamic Pressure sensor selected.
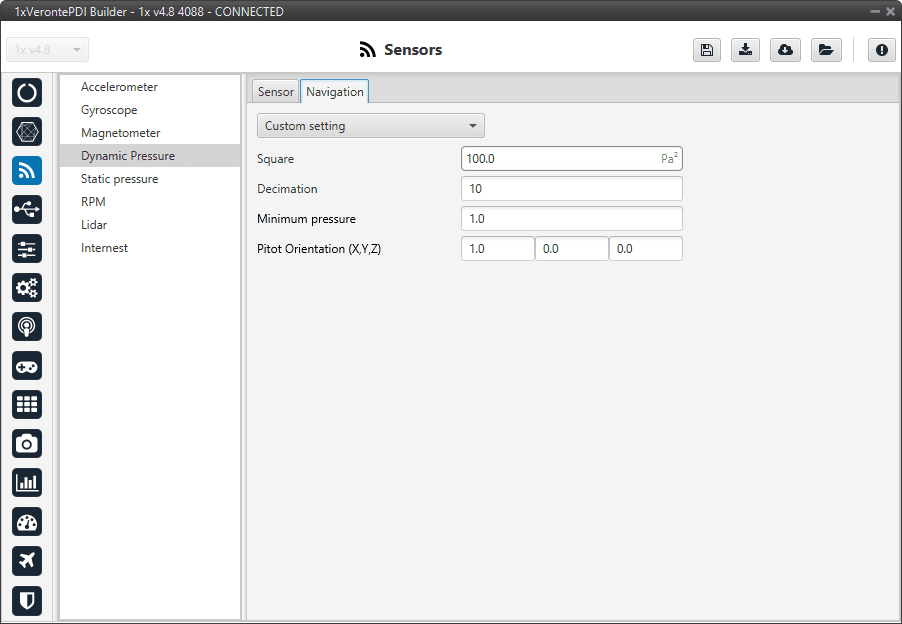
Dynamic Pressure menu - Navigation parameters¶
Enable: User can choose from Disabled, values from the sensor will be received, but they will not enter the Navigation Filter, or Custom settings, which will take into account all the following parameters.
Square Error: Sensor error square, which defined the weight if the measurement into the Navigation filter.
Decimation: Defines the bunch of data from which 1 value will be stored. For example, if decimation is 10, every 10 measurements 1 will be taken into account. This procedure is used to reduce the number of samples.
Minimum pressure: Minimum pressure readable from the sensor.
Pitot Orientation: Vector defining the Pitot orientation on the platform.
Internal
This menu displays the posible parameters that can be configured for the internal Dynamic Pressure sensor.
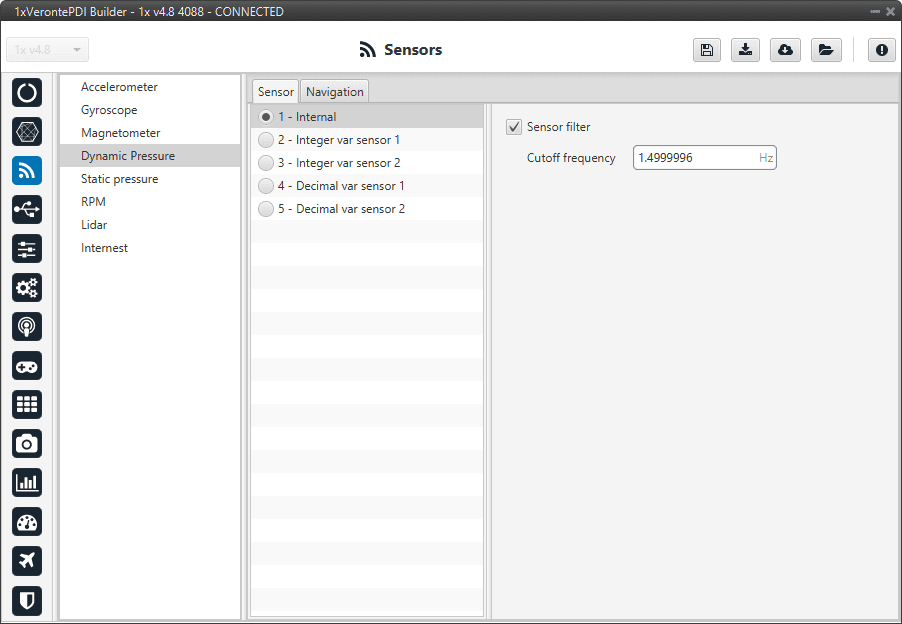
Internal dynamic pressure sensor menu¶
In this menu it is possible to set different options regarding filters.
Digital filter: Enables a low pass filter which its cutoff frequency is configured manually, allowing the user to input any desired value in Hz. It is a software filter.
Integer var sensor 1-2
In this menu it is possible to configure integer variables provided by an external sensor.
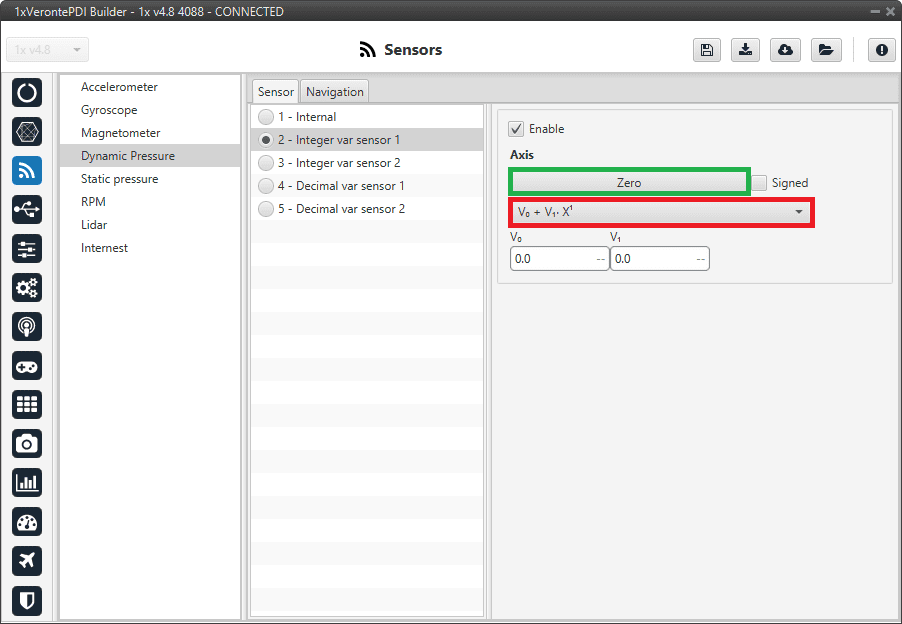
Integer var dynamic pressure sensor menu¶
When Integer var sensor 1 or 2 are selected, the previous panel will be shown. In this panel, the user selects the variable that has been stored in a user variable (Green Box) and the operations that will be carried on (Red Box). It is possible to use the signal through a linear or quadratic relation. The following image shows an example of a linear relation:
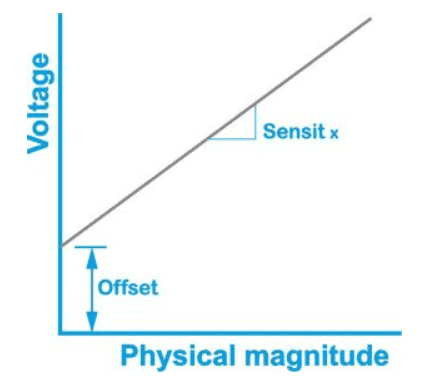
Linear relation of 2 variables¶
In addition, users must indicate whether the integer value is with sign or without sign. That is, if the “Signed” box is:
Enabled: Integer value with sign.
Disabled: Integer value without sign.
The process of configuration has to be done using custom messages. This is to be configured in the Custom Messages menu of the I/O section. The configuration will depends on the device in use and its communication protocol.
Decimal var sensor 1-2
In this menu, the user selects a real variable, this does not requiere a signal treatment. The process of configuration is similar to the one carried out when configuring a Integer Variable.
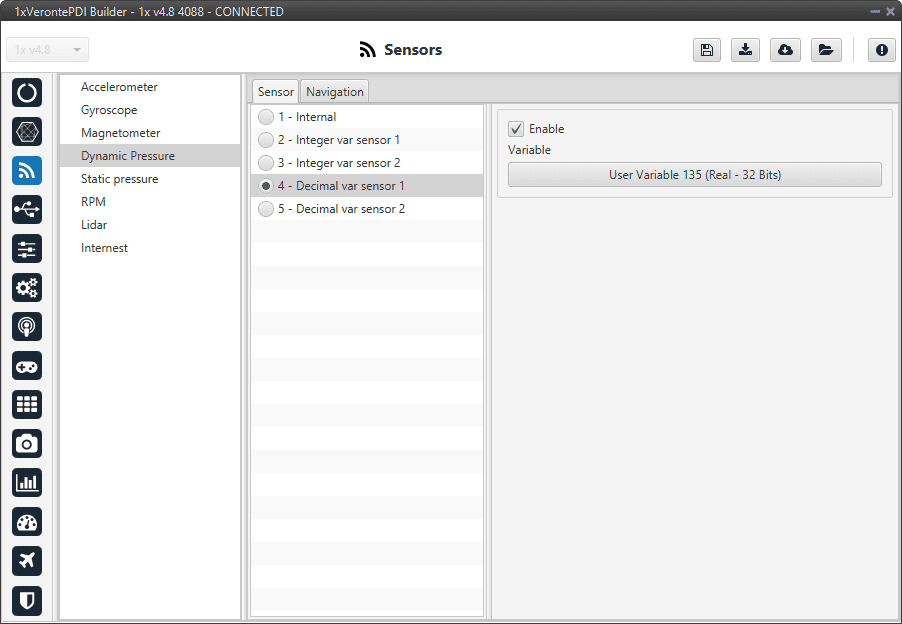
Decimal var dynamic pressure sensor menu¶
Static Pressure¶
1x autopilot has three pressure input lines, two for static pressure to determine the absolute pressure and one for pitot in order to determine the dynamic pressure.
This menu allows the user to configure a static pressure sensor input in 1x.
The user can choose between 3 types of source:
Internal (HSC/MS56/DPS310): 1x autopilot uses the internal sensor.
Integer var sensor 1-2: 1x autopilot uses a integer value provided by an external sensor.
Decimal var sensor 1-2: 1x autopilot uses a decimal value provided by an external sensor.
Important
In this section, the user can only modify some configurable parameters, the selection of the static pressure sensor and the configuration of the Variance are done in Static Pressure Sensor - Block Programs section.
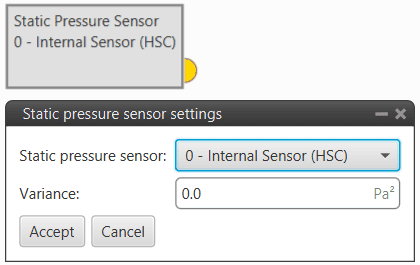
Static Pressure sensor block¶
Atmospheric calibration export
The Atmospheric calibration export allows, in a standard ground-air configuration, to continuously send information regarding the static pressure configured on the ground platform to the desired air platform. Therefore, it is a configuration that must be performed on the Veronte Autopilot 1x ground unit.
This function is useful when making long flights as the static pressure varies significantly throughout the day and therefore the altitude estimation will also vary.
Warning
For correct operation both Veronte Autopilots 1x (ground and air units) must measure the same pressure at the same height (this must be checked).
This option is configured independently fo the selected the Static Pressure sensor.
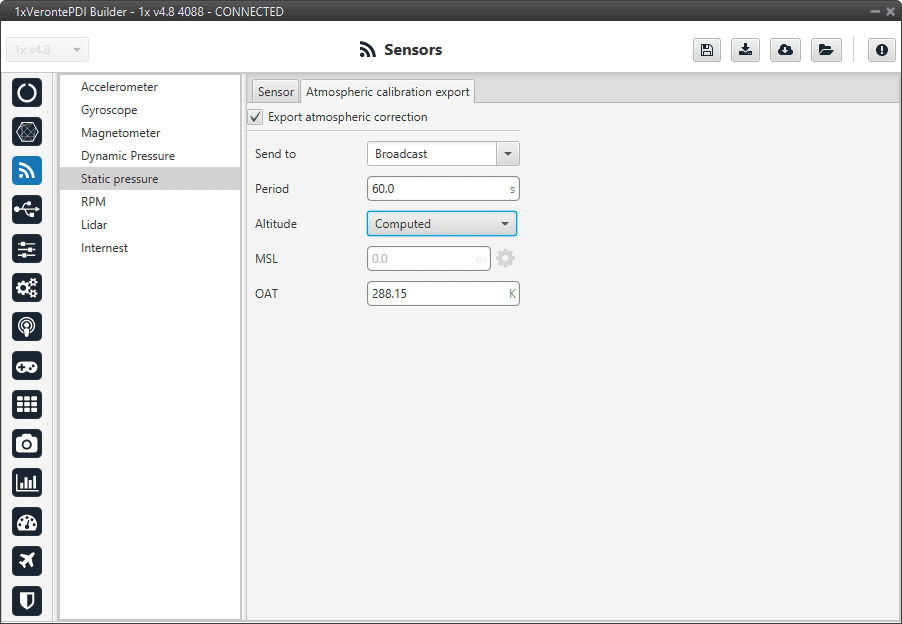
Static Pressure menu - Atmospheric calibration export parameters¶
Export atmospheric correction: Enables this feature.
This menu has 5 parameters that need to be configured:
Send to: Points where the correction will be sent. It can be another 1x unit (Address of another 1x autopilot), Broadcast or App 2.
Period: Period of time spent between sending each correction.
Altitude: There are 2 options available for this parameter:
External: Users can manually enter the altitude if known.
Computed: By selecting this option, the altitude will be computed by the system.
Warning
When this option is selected, it is necessary to add an automation in the 1x ground unit to calibrate the atmosphere periodically (see Atmosphere Calibration action), to prevent the MSL from drifting.
MSL: Can be entered manually or by a system variable.
Important
This parameter is only enabled when the External option is selected as Altitude.
OAT: Outside Atmospheric Temperature, to be defined by the user.
Internal Sensor HSC/MS56/DPS310
This menu displays the posible parameters that can be configured for the internal Static Pressure sensors.
1x autopilot has embedded 3 digital static pressure sensors: the DPS310, the MS56 and the HSC. See more information on the pressure ports in Hardware installation - Electrical.
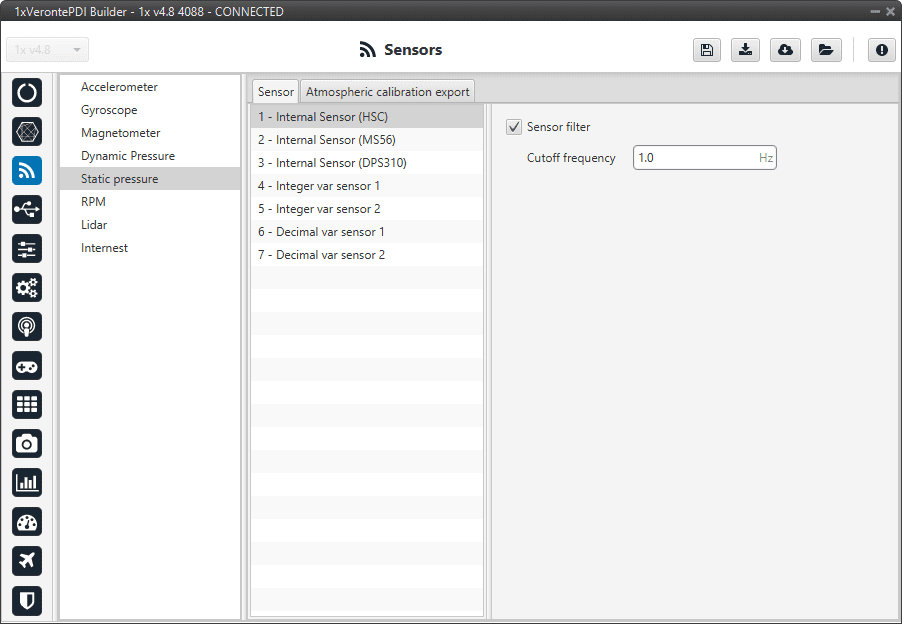
Internal Static Pressure sensor menu¶
In this menu it is possible to set different options regarding filters.
Sensor filter: Enables a low pass filter which its cutoff frequency is configured manually, allowing the user to input any desired value in Hz. It is a software filter.
Integer var sensor 1-2
In this menu it is possible to configure integer variables provided by an external sensor.
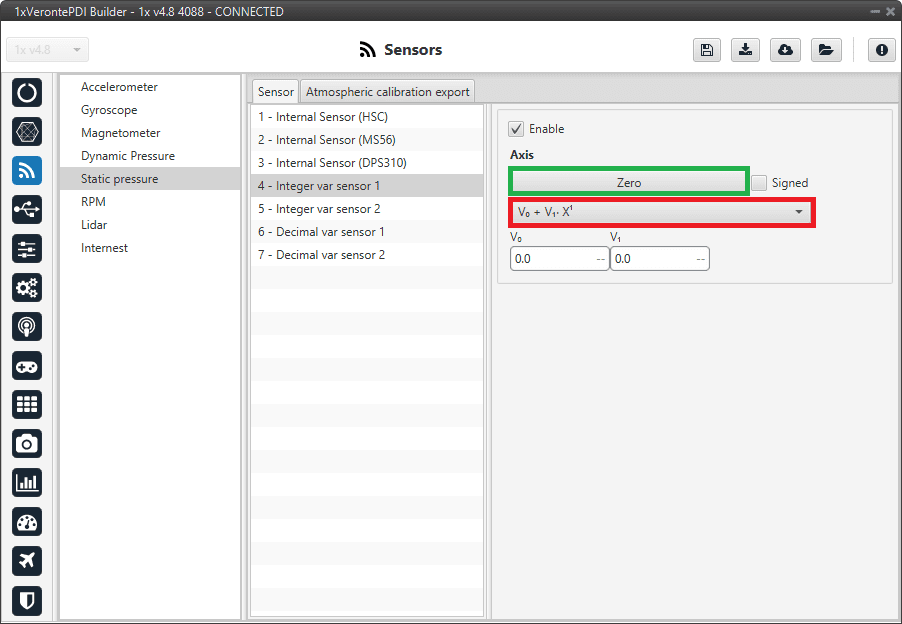
Integer var static pressure sensor menu¶
When Integer var sensor 1 or 2 are selected, the previous panel will be shown. In this panel, the user selects the variable that has been stored in a user variable (Green Box) and the operations that will be carried on (Red Box). It is possible to use the signal through a linear or quadratic relation. The following image shows an example of a linear relation:
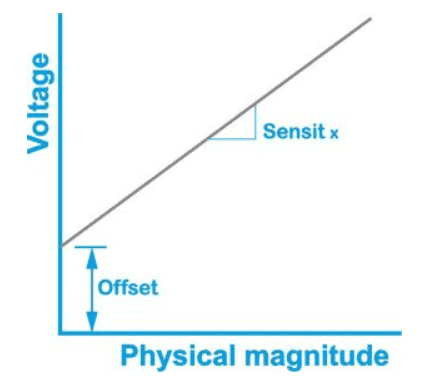
Linear relation of 2 variables¶
In addition, users must indicate whether the integer value is with sign or without sign. That is, if the “Signed” box is:
Enabled: Integer value with sign.
Disabled: Integer value without sign.
The process of configuration has to be done using custom messages. This is to be configured in the Custom Messages menu of the I/O section. The configuration will depends on the device in use and its communication protocol.
Decimal var sensor 1-2
In this menu, the user selects a real variable, this does not requiere a signal treatment. The process of configuration is similar to the one carried out when configuring a Integer Variable.
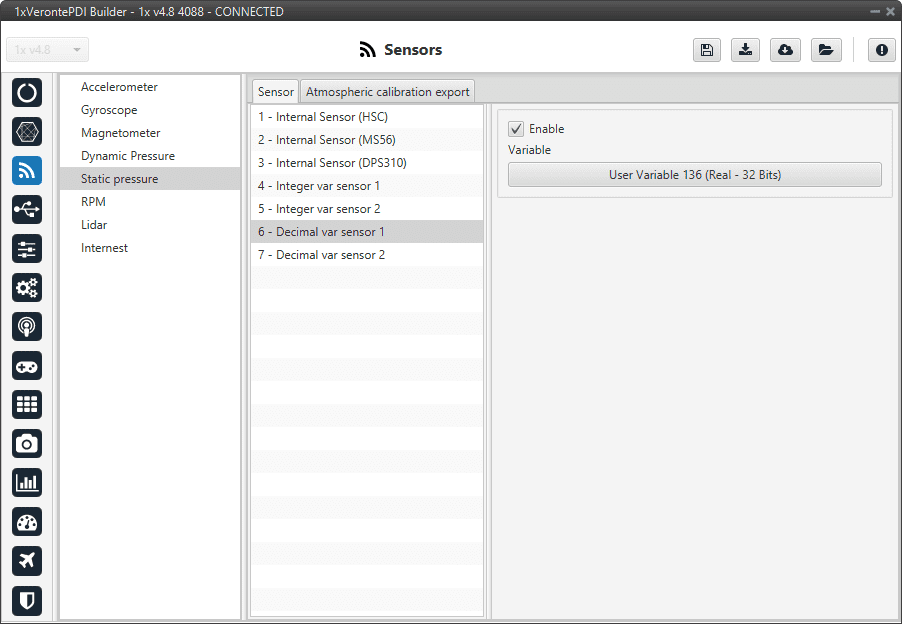
Decimal var static pressure sensor menu¶
RPM¶
1x autopilot can measure RPMs by measuring from up to 6 input sources:
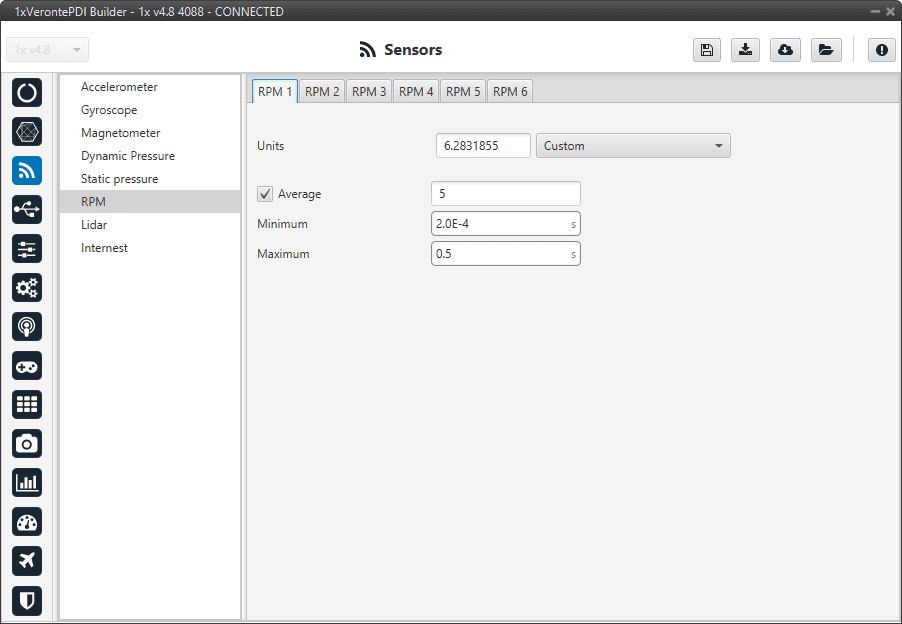
RPM menu¶
Units: Sensor conversion factor. It can be Custom, Radians per pulse or Pulse per cycle.
Average filter (Measures): It is a filter to avoid voltage spikes.
Minimum pulse: Minimum time to detect a lap.
Maximum time without capture: The maximum period of time allowed without capturing.
Lidar¶
The I2C bus allows the connection of several devices with different addresses to the same line via master-slave communication. At this moment, 1x autopilot supports the following Lidar devices:
Garmin LIDAR-Lite v3: Optical distance measurement sensor with a range of 5cm to 40m.
SF11 Lidar: Long range laser altimeter. Supported SF11/B and SF11/C with a range of maximum 50m and 0.2m to 120m respectively.
SF20 Lidar: OEM laser altimeter module. Supported SF20/C with a range of 0.2m to 100m.
1x allows up to 5 Lidar devices to be connected to the system at the same time. The configuration menu can be seen below:
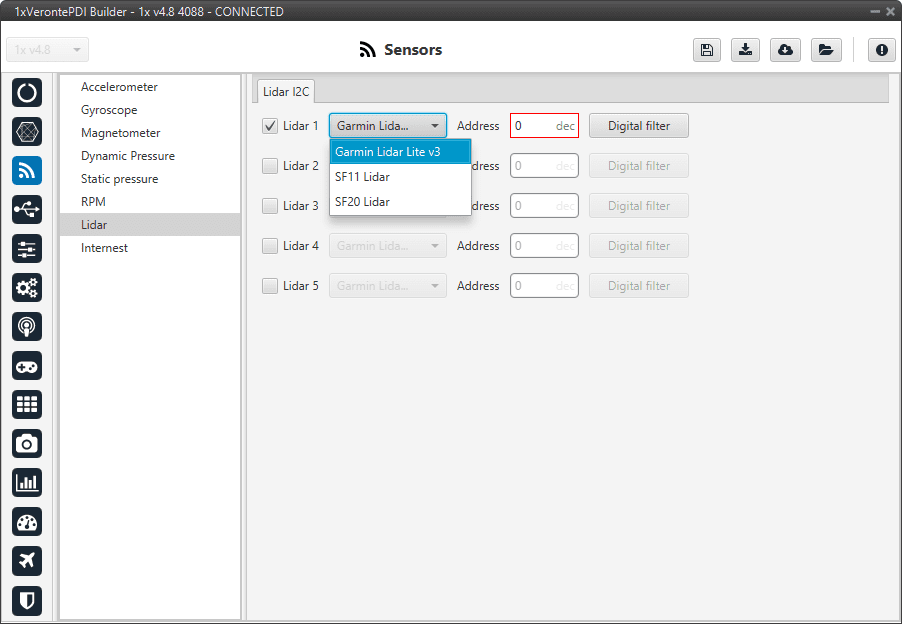
Lidar devices¶
After enabling the needed number of Lidar devices, configurable parameters are:
Type of Lidar.
Address: With an accepted value between 16 - 239, this is the origin address from the Lidar being configured.
Digital filter: Enables a low pass filter which its cutoff frequency is configured manually, allowing the user to input any desired value in Hz. It is a software filter.
Warning
I2C address will be different for different devices make sure to define it properly by checking the manufacturer documentation.
Note
The Lidar number (Lidar 1/5) needs to be kept in order to properly configure the Altimeter later (Altimers sensors - Block Programs section).
Internest¶
An ultrasound sensor computes Veronte Autopilot 1x position by measuring the time the signal sent out takes to return. The following panel together with Relative position sensor block (see Relative position sensor - Block Programs section) allows the user to configure an Internest system with Veronte Autopilot 1x.
This menu allows the user to choose the version of Internest to be used, its range and the rotation matrix:
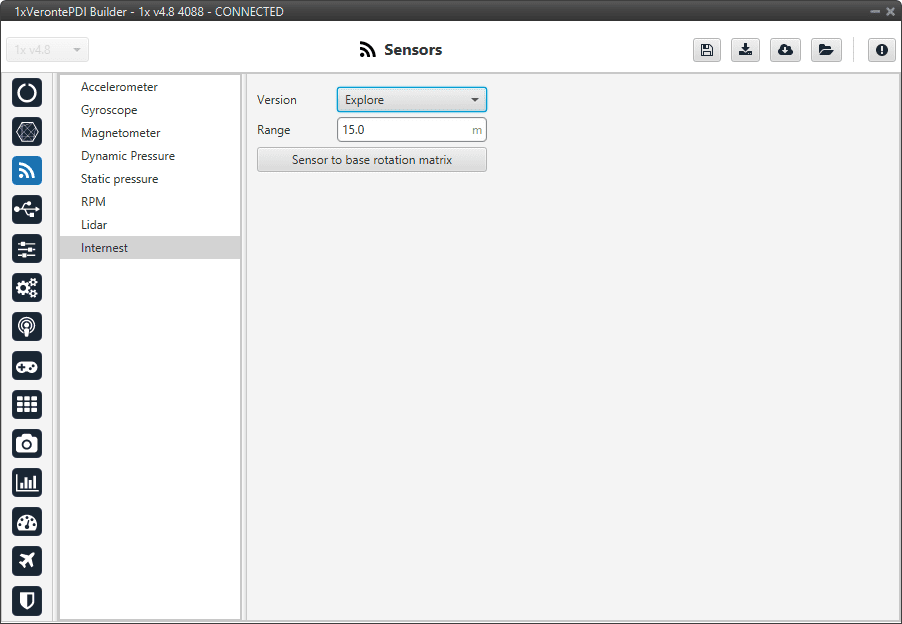
Internest menu¶
Version: Users must choose the version of the Internest system, the available options are Base and Explore.
Range: Defines the distance at which Internest values will start to be valid.
Sensor to base: Matrix to rotate the system to match the Veronte Autopilot 1x coordinate system.
Internest - Rotation matrix¶